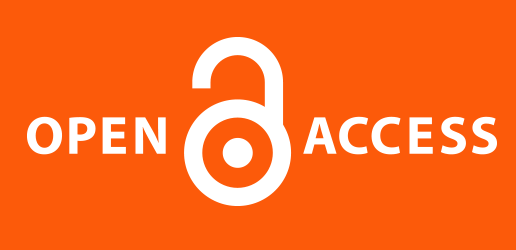
智能技术在煤矿电气工程自动化中的应用
摘要
我国煤矿高效率开采作业离不开电气工程的合理建设,得益于智能化技术的融合运用,能够在保障电气工程自动化、高效化运行的同时,缩减人力资源来提升煤矿开采成本控制效果。本文从智能化技术应用优势的分析入手,并阐明电气工程自动化中智能技术的实践应用。
我国能源结构中煤炭资源占据重要地位,据中国煤炭工业协会数据调查表明,截止到2022年我国煤炭产量增长至45.6亿吨,不仅是我国化工、钢铁、电力等行业可持续发展的重要支持,亦对我国社会和谐发展有着重要影响。而传统电气工程自动化无法满足实际开采需求,甚至因系统设备故障频繁出现影响到开采安全。得益于智能化技术的融合应用,可做到对煤矿开采作业过程的实时、全面控制,以保证煤炭开采符合安全化、智能化要求。鉴于此,探讨电气工程自动化中智能技术的实践应用,对推动煤矿行业稳定、长久发展有着重要影响。
1 智能化技术应用优势分析
煤矿开采中智能化技术应用发挥至关重要作用,主要表现为:
一是提升生产效率。以往煤矿开采涉及到对大量人力资源的运用,其开采效率受到人员熟练程度、操作经验等方面的直接影响。得益于智能化技术的融合运用,可采取自动化、智能化手段来降低人为因素影响,如在开采作业阶段利用智能采煤机对煤层厚度、硬度等信息的实时采集,通过信息获取对割煤参数进行智能化、自动化调整,避免采煤效率受到割煤不精准的影响[1]。
二是加强安全保障。煤炭开采出现透水事故、瓦斯爆炸、顶板坍塌等隐患的概率较大,轻则因事故发生导致煤炭开采停工,重则对开采人员生命安全产生较大威胁。通过对智能化技术的有效应用,可依托于智能化监控平台对井下环境参数实时监控,结合对传感器的布置对井下一氧化碳浓度、温湿度、瓦斯浓度等数据信息的全面采集,若数据超出阈值第一时间发出警报,为后续安全管理、救援等工作的有效开展提供支持[2]。
三是提升资源利用率。以往煤矿开采中煤炭资源浪费现象频繁出现,对此可借助智能化技术对生产数据进行监控、分析,为资源的高效化利用提供支持。在实际开采作业过程中,可依托于大数据技术对开采数据进行综合分析、处理,依据分析结果对开采方案加以优化,以实现对煤炭资源回收率的显著提升。另外,可根据煤炭产量情况对智能运输系统加以配置,通过对运输设备的合理调度来减少煤炭与资源损耗[3]。
四是提升系统自适应能力。当前煤炭开采普遍存在地质、环境复杂等因素影响,而常规自动化系统的构件无法对开采地质条件加以适应,通过对先进算法、模型的合理应用,可支持对环境变化的实时化、动态化感知,以实现对系统参数与运行模式的自动化调整,确保电气工程自动化系统能够适应不同生产条件。如煤炭开采作业受地质构造变化的影响,可利用智能采煤机对割煤策略进行合理调整,继而为采煤作业的顺利开展提供支持。
2 煤矿电气工程自动化中智能技术应用
2.1数据采集与监控系统设计
通过对智能化技术的集成应用,可实现对煤矿开采作业的有效监控。对此可依据实际开采需求的分析,对数据采集与监控系统进行优化设计。以某矿业一号煤矿为例,在智能技术引入前井下供电系统监测采用人工值守、综合保护器就地操作模式。次模式受人为因素影响较大,监测结果准确性和可靠性难以保证。由于煤矿井下中变电所与采煤区的变电所布置集中性较差,移动变电站随着工作面的掘进需要实时移动,频繁通断电会产生较大的电压电流冲击。加上井下运行环境恶劣,供电系统故障频发[4]。一旦发生故障,严重影响煤矿正常生产。为解决上述问题,该煤矿需借助智能化技术对井下供电系统加以改进,该智能监控体系地面主控站、井下监测节点及电力监测终端构成。其中地面主控站部署专业级供电系统组态平台,集成实时动态监控、数据统计分析与远程调控等核心功能。操作人员通过可视化界面可清晰掌握井下电网运行态势,及时追踪电压波动、电流强度及功率因数等关键指标。而井下监测节点承担信息中转枢纽职能,既对接地面主控系统又连接底层监测终端。其具备高压开关保护装置控制能力,集成故障波形记录、信息传输存储及供电网络监控等多元功能。当井下电网发生异常时,该节点能快速捕获故障特征信号并上传至地面控制中心,为应急处置提供决策依据。电力监测终端专司变电所设备运行参数采集任务,持续获取电压数值、电流强度、温升数据等实时信息,并上传至井下监测节点[5]。该终端同时具备接收控制指令能力,可执行远程设备启停操作,有效提升设备管理响应速度与操作灵活性。硬件架构层面,调度中枢、地面主控平台与井下监测节点均采用高性能硬件平台。调度中枢配置高算力服务器集群,具备海量数据处理与存储能力;地面主控系统配置工业级显示屏与冗余通信模块,确保监测画面实时刷新;井下节点采用本质安全型设备,满足矿井特殊环境防护要求,保障数据采集传输可靠性。为验证设计完成井下电力监控系统的应用效果,在改煤矿进行为期半年试运行,并对相关数据进行跟踪记录。结果表明该智能数据采集与监控系统运行稳定可靠,能够满足设计要并,实现井下供电系统的实时监测与历史数据存储调用。通过调用部分中高压历史数据曲线,可清晰地观察到电压变化趋势,为供电系统维修人员进行故障诊断与排查提供支持[6]。
2.2 高效电机控制系统
煤矿开采作业中涉及到对采煤机、通风机、刮板输送机等关键设备的运用,而以往电气工程依赖于继电器-接触器控制的应用。在运行期间能耗问题尤为突出,传统电机控制系统在运行过程中,其电机无法根据实际负载情况进行精准调速,经常处于满负荷运行状态导致大量电能浪费。且控制精度不理想,传统控制系统难以满足现代煤矿生产高精度要求[7]。在采煤机作业时无法精确控制电机转速,采煤机割煤速度控制不符合要求,不仅对煤炭开采质量产生较大影响,还易造成煤炭资源大量浪费。煤层厚度变化较大区域采煤机无法做到对割煤速度的及时调整,导致部分煤炭未能被充分开采,致使煤炭资源回收率始终处于较低状态。对此可借助智能电机控制技术对系统运行加以改进,如依托于智能电机控制器对电机电流、电压、转速、温度等参数加以采集,将上述数据传输到微处理器中,微处理器利用智能控制算法对数据进行分析和处理。当检测到电机负载发生变化时智能控制算法会根据预设的控制策略,自动调整电机的运行参数,将设备运行控制在最佳运行状态。若电机负载降低智能控制器会降低电机转速,减少电能消耗;当电机负载增加时,智能控制器会相应提高电机的转速,确保电机能够稳定运行。对于变频调速技术的应用,则是通过改变电机电源频率,实现电机转速的连续调节。在刮板输送机运行过程中,变频调速技术可根据输送煤炭的量实时调整电机转速。当煤炭输送量较少时,通过对电机转速加以控制来减少能源消耗;当煤炭输送量增加时,提高电机转速来保障煤炭的及时输送。相较于传统恒速运行方式的应用,变频调速技术可支持电机在不同的工况下保持高效运行状态,以实现对能源利用效率的显著提升。另外智能电机控制系统具备远程监控和故障诊断功能,基于对煤矿的监控网络的有机连接,管理人员可在地面控制中心实时监控电的运行状态,对电机进行远程操作和控制。电机出现故障时系统自动诊断故障原因并及时发出警报,通知维修人员进行处理,以实现对故障排查和修复时间的有效缩短[8]。
2.3 自动化工作面控制系统
通过对智能技术的集成应用,可助力煤矿开采作业朝着智能化、自动化方向持续迈进。某大型煤矿年产量达1000万吨以上。在传统的采煤作业模式下,人工操作占据主导地位,导致采煤效率受到较大限制。且开采期间采煤机割煤速度、截割深度等参数调整依赖人工经验判断,难以根据煤层变化实时精准调整,导致煤炭开采质量不符合预期要求,且资源回收率始终未得到提升。再加上煤矿井下环境复杂恶劣,出现瓦斯泄漏、顶板坍塌、透水等安全隐患的概率较大。人工操作过程中工作人员难以全面、及时监测各种安全风险,一旦发生安全事故极易造成严重人员伤亡和财产损失。为提高煤矿生产安全性和效率,该煤矿决定进行工作面自动化改造,引入智能技术来实现采煤机、刮板输送机、液压支架等设备的协同自动化作业,提高煤炭开采精准度和连续性[9]。结合对安全监测和预警系统的构建,可做到对井下环境参数和设备运行状态的实时监测,及时发现并处理安全隐患。改造期间该煤矿对井下设备进行全面升级。加大对智能采煤机的应用力度,该采煤机配备高精度传感器和智能控制系统,能够实时感知煤层厚度、硬度、倾角等地质信息,并根据采集信息自动调整割煤速度、截割深度和牵引速度,以推动割煤作业的精准化、智能化开展。并对刮板输送机和液压支架进行智能化改造,使其能够与采煤机实现协同作业,确保其采煤工作面的整体运行效率得到显著提升。另外,该煤矿构建高速、稳定工业以太网和无线通信网络,实现井下设备与地面控制中心之间数据实时传输和远程控制。依托于通信网络地面控制中心可实时获取井下设备运行状态、位置信息等数据,并对设备进行远程操作和控制,以促进生产管理效率和灵活性的显著提升。结合对智能化采煤工作面控制系统软件的开发,可集成设备监控、生产调度、安全管理等多个功能模块,实现对采煤作业全面智能化管理。工作人员可在地面控制中心实时监控采煤工作面的设备运行状态、生产进度等信息,并根据实际情况进行远程调度和控制,继而为煤矿安全、高效开展提供支持。
此外,该煤矿依托系统集成技术,对采煤机、刮板输送机、液压支架、破碎机、转载机等设备进行集成控制。其中硬件主要依托于标准化接口和通信协议,实现各设备之间物理连接和数据传输。采煤机与刮板输送机之间依托于专用通信电缆连接,以促进采煤机割煤过程中与刮板输送机的协同运行,继而为煤炭及时、顺利输送提供保障。而软件系统则是对统一设备控制平台的有效开发,对设备运行参数进行集中管理、控制。依托于该平台人员可对采煤机割煤速度、截割深度进行有效调整,并支持对刮板输送机运输速度,液压支架升降、推移等参数进行统一设置、调整,以设备协同工作的形式来提升煤矿开采效率。该煤矿中自动化工作面控制系统的应用,煤矿生产效率得到显著提升[10]。开采期间智能采煤机可根据煤层变化实时调整割煤参数,实现高效、精准的割煤作业,采煤效率比改造前提高30%以上。且刮板输送机和液压支架的协同自动化作业,可显著提高采煤工作面整体运行效率,减少设备空转时间和故障停机时间。据统计,改造后该煤矿煤炭年产量从1000万吨提高至1300万吨以上且增长30%,继而为煤矿企业增大经济效益获取提供支持。
结束语
综上所述,煤矿电气工程自动化中合理运用智能化技术,可在提升煤矿开采效率与质量的同时,为井下开采安全保障提供技术支持。鉴于此,需在明确智能化技术应用优势的基础上,对煤矿开采环境条件、技术要求等方面进行深度剖析,基于对人工智能、大数据、物联网等智能技术的集成应用,在电气工程自动化各环节积极引进智能化技术,以促进开采作业的智能化、自动化开展,为煤矿企业增大经济效益获取提供保障
参考文献
[1]朱健.智能技术在煤矿电气工程自动化中的应用探究[J].轻松学电脑,2021,000(011):P.1-2.
[2]赵文军.智能技术在煤矿电气工程自动化中的应用[J].中国科技纵横,2020,000(021):40-41.
[3]陈瑞婷.智能化技术在煤矿电气工程自动化中的应用探究[J].矿业装备,2024(4):67-69.
[4]韩海君.煤矿电气工程自动化中智能技术的应用分析[J].西部探矿工程,2023,35(9):133-135.
[5]戴学伟.智能化技术在煤矿电气工程自动化中的应用研究[J].矿业装备,2024(3):134-136.
[6]韩小轩.智能化技术在煤矿电气工程自动化中的应用[J].探索科学,2021(6):242-242.
[7]杨辉,王文强,南雄,等.智能化技术在煤矿电气工程自动化中的应用[J].科学大众,2021,000(008):182-183.
[8]高亚超.煤矿电气工程自动化中智能技术的运用路径探究[J].企业科技与发展,2021(10):58-60.
[9]曹振洋.煤矿电气工程及其自动化的智能化技术应用研究[J].进展:科学视界,2023(2):117-119.
[10]程智鹏.智能化技术在矿山电气工程自动化控制中的应用[J].内蒙古煤炭经济,2023(8):112-114.
如何引用
参考
朱健.智能技术在煤矿电气工程自动化中的应用探究[J].轻松学电脑,2021,000(011):P.1-2.
赵文军.智能技术在煤矿电气工程自动化中的应用[J].中国科技纵横,2020,000(021):40-41.
陈瑞婷.智能化技术在煤矿电气工程自动化中的应用探究[J].矿业装备,2024(4):67-69.
韩海君.煤矿电气工程自动化中智能技术的应用分析[J].西部探矿工程,2023,35(9):133-135.
戴学伟.智能化技术在煤矿电气工程自动化中的应用研究[J].矿业装备,2024(3):134-136.
韩小轩.智能化技术在煤矿电气工程自动化中的应用[J].探索科学,2021(6):242-242.
杨辉,王文强,南雄,等.智能化技术在煤矿电气工程自动化中的应用[J].科学大众,2021,000(008):182-183.
高亚超.煤矿电气工程自动化中智能技术的运用路径探究[J].企业科技与发展,2021(10):58-60.
曹振洋.煤矿电气工程及其自动化的智能化技术应用研究[J].进展:科学视界,2023(2):117-119.
程智鹏.智能化技术在矿山电气工程自动化控制中的应用[J].内蒙古煤炭经济,2023(8):112-114.
版权
未提供许可协议