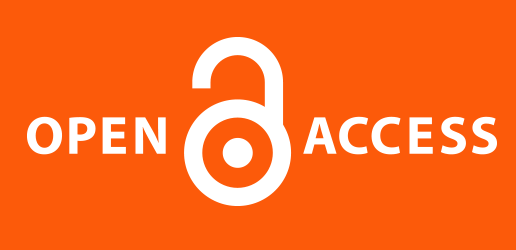
热轧及正火钢的焊接技术研究
摘要
热轧及正火钢因其优良的力学性能和经济性,在建筑、桥梁、机械制造等领域得到广泛应用。然而,这类钢材的焊接性较为复杂,焊接过程中易出现裂纹、热影响区性能变化等问题。本文系统分析了热轧及正火钢的成分、性能、焊接性以及焊接工艺要点,重点探讨了焊接裂纹的产生原因及预防措施、热影响区性能变化的影响因素,以及典型钢种 Q345 的焊接工艺要点,旨在为工程实践提供理论支持和技术指导。
引言
热轧及正火钢是一类重要的工程结构用钢,广泛应用于建筑、桥梁、机械制造和能源输送等领域。随着工业技术的不断发展,对这类钢材的焊接技术提出了更高的要求。焊接过程中,热轧及正火钢的焊接性、热影响区性能变化以及焊接工艺参数的控制等因素,直接影响焊接质量和结构的安全性。因此,深入研究热轧及正火钢的焊接技术具有重要的理论意义和实际应用价值。
1 热轧及正火钢的成分与性能
1.1 热轧钢材特性
热轧工艺制造的钢材抗拉强度范围一般多为为295~390兆帕,其主要合金体系为碳-锰或碳-锰-硅系。该类型钢材的强度指标主要依赖于锰、硅元素在铁基固溶体中的强化效应。在碳含量较低(≤0.20%)的工艺条件下,当锰元素含量控制在1.6%以下、硅含量不超过0.6%时,材料可保持优良的塑性变形能力和冲击韧性。如果超出此成分区间,将导致材料延展性能显著下降。基于此,热轧钢的合金配比与强度提升存在明确的含量限制。
此类钢材因具备良好的综合力学特性、加工成形性能以及经济性优势,在工程领域获得广泛应用。以Q345(16Mn)为例,自1957年以后得到广泛应用,比如在南京长江大桥以及国产万吨级远洋货轮等,各大重大工程中都有成功应用[1]。
现行标准将按锰、硅含量差异,Q345划分为A-E五个质量等级:Q345A对应原16Mn牌号,Q345C则等效于锅炉压力容器专用钢材16Mng与16MnR。热轧态组织呈现铁素体与珠光体复合结构,对于大截面构件可通过正火工艺改善组织均匀性,此处理虽使材料强度微量下降,但能显著提升塑性指标。
1.2 正火强化钢材
当钢材的屈服强度超过390兆帕时,单纯依靠固溶强化机制已无法实现工程需求。采用正火工艺,在基础合金体系上添加钒、钛、铌等碳氮化物,通过沉淀强化与细晶强化作用实现提升物理性能和力学性能。正火工艺的关键作用在于促进过饱和固溶体中微合金元素的时效析出,同时通过相变重结晶实现组织细化。
1.3 控轧微合金化
现代轧钢技术发展的阶段代表——微合金控轧钢,是采用微量合金添加(总含量约0.1%)与控轧工艺协同控制的新模式。通过钒、钛、铌等微合金元素的精准调控,配合轧制过程中的形变诱导析出与动态再结晶控制,实现晶粒细化与结构强化的双重效果[2]。生产工艺方面,采用低碳低硫低夹杂物含量控制等钢水纯净度提升等先进技术,确保材料获得超细晶组织结构。此类钢材兼具高强度、优异低温韧性及良好焊接特性,已成功应用于X60至X70系列高等级油气输送管线工程。
2 热轧及正火钢焊接性能分析
热轧及正火钢整体焊接性能优良,这是因为碳及合金元素含量相对较低,随着合金配比的提高,焊接性变差。在焊接过程中,需着重关注裂纹形成及热影响区组织演变规律[3]。
2.1 焊接裂纹形成机理
2.1.1 低温裂纹(冷裂纹)
淬硬组织生成、结构约束状态及氢元素扩散,这是冷裂纹的三要素。冷裂纹就是在这三个条件变化下形成的。钢材淬硬趋势可通过碳当量公式(CE=Pcm)、热影响区维氏硬度等参数判断和评估。当CE值小于0.4%时,材料焊接过程中不易形成淬硬相,常规工况下无需特殊工艺措施。典型屈服强度295-390MPa级热轧钢的CE值普遍低于此临界值,仅在特大厚度构件(δ≥50mm)或极端低温环境需考虑预热处理;对于440-490MPa级正火钢,其CE值通常处于0.4%-0.6%区间,当板厚超过25mm时必须采用预热工艺以控制冷裂纹风险。
2.1.2 高温裂纹(热裂纹)
热轧及正火钢通过提升Mn/S比值(≥40)有效抑制晶间裂纹产生。在标准成分控制及规范焊接参数条件下,此类钢材具有优良的抗热裂性能。特殊工况下,如母材出现碳硫共偏析时,可通过优化焊接材料选择(低C高Mn焊材)及调整熔池混合比(≤15%)实现裂纹预防。
2.1.3 再热致裂现象
含钼铬元素的合金钢在焊后热处理(580-650℃)或高温加热时,热影响区粗晶带易产生沿熔合线分布的微裂纹。即消除应力裂纹,也称再热裂纹。研究表明,18MnMoNb等材料在拘束应力超过300MPa时具有再热裂纹倾向。工程实践中采用阶梯式预热(200℃×2h)或焊后消氢处理(250℃×4h)可有效缓解此类缺陷。
2.1.4 层状撕裂控制
层状撕裂缺陷与冶金和压力加工质量及物理形状密切相关,比方板厚、接头形式和 Z 向应力等,主要受硫元素偏析(≤0.005%)及Z向断面收缩率(ψZ)影响。当ψZ值超过25%时,层状撕裂风险显著降低。重大工程结构中采用Z向增强钢(如ASTM A572 Gr.D36),通过特殊工艺将ψZ提升至55%以上,但生产成本相应也增加约30%[4]。
2.2 热影响区组织性能变化
热轧及正火钢焊接热影响区性能变化,指的是过热区的脆化以及在一些合金元素含量较低的钢中可能出现的热应变脆化问题。
2.2.1 过热区韧性退化
在峰值温度超过Ac3的过热区域,奥氏体晶粒异常长大(≥ASTM No.3)及第二相粒子溶解导致冷却过程中形成脆性组织。热轧钢主要因魏氏体(Widmanstätten)结构(体积分数>15%)引发脆化,而正火钢的脆化机理则源于微合金元素(V、Ti)碳氮化物的高温分解。正火钢过热区脆化与魏氏组织无关,除晶粒粗化外,主要是由于在 1200℃高温下,起沉淀强化作用的碳化物和氮化物质点分解并熔于奥氏体,在随后的冷却过程中来不及析出而固溶在基体中,导致铁素体基体的硬度上升而韧性下降。采用窄间隙焊接(热输入≤15kJ/cm)可限制高温停留时间(t8/5<8s),使碳氮化物保留率提升至70%以上,显著改善韧性指标[5]。
2.2.2 热应变脆化
在200-400℃温区,焊接残余应变与氮原子扩散共同作用引发动态应变时效现象。C-Mn系钢材(如Q345)在经历2%塑性应变后,其夏比冲击功可能下降40%。通过微合金化处理(添加0.02%Ti或0.05%Al)可将固溶氮含量控制在20ppm以下,经600℃×1h退火处理后,韧性恢复率可达95%以上。对比试验显示,Q420钢因含钒氮化物形成元素,其热应变脆化敏感性较Q345降低约60%。
3 热轧及正火钢焊接工艺控制
3.1 焊接工艺选择策略
该类钢材具有工艺选择多样性,常规焊接方法包括手工电弧焊(SMAW)、埋弧自动焊(SAW)、活性气体保护焊(GMAW)及电渣焊(ESW)等。实际工程应用中需结合构件几何特征、生产规模及经济性进行综合决策。以船体结构焊接为例,手工电弧焊凭借空间适应性优势(全位置焊接能力)广泛应用于复杂节点,而埋弧焊凭借高达8-12mm/s的焊接速度,成为平板纵缝的首选工艺。需注意电渣焊虽具有60mm以上厚板单道成型能力,但易引发粗晶脆化问题。
3.2 预制加工技术规范
材料预处理阶段需遵循以下准则:①切割工艺优先采用数控等离子切割(公差±0.5mm)或激光切割(粗糙度Ra≤12.5μm),对于屈服强度≥420MPa的厚板(δ≥40mm),切割后需进行磁粉检测(MT)排除微裂纹;②坡口制备时,火焰切割面需经砂轮打磨至Sa2.5级清洁度,V型坡口角度控制在60°±5°范围内;③定位焊实施前需在坡口两侧30mm范围内进行丙酮脱脂处理,定位焊缝长度遵循L≥max(50mm,4δ)原则,并采用脉冲电流模式(基值电流降低20%)抑制起弧裂纹[6]。
3.3 焊材适配性原则
焊材选型需满足两项要求:冶金相容性与力学匹配性。具体内容包括:①基于强度匹配原则,采用等强或微低强设计(Δσ≤50MPa),如Q420钢配套E5515焊条(熔敷金属σb=550-610MPa);②熔合比动态调控,薄板焊接(δ≤6mm)时选用降强型焊材(降幅15%),厚板多层焊时采用阶梯式强度匹配;③特殊工况补偿设计,对于焊后需正火处理的接头,选材强度需预留10%余量。有案例显示,焊接16MnCu耐候钢时,采用Cu含量0.3%-0.5%的ECu焊丝可使焊缝耐蚀性与母材保持同步。
3.4 工艺参数优化
3.4.1 热输入量控制原则
热输入量(Q=ηUI/v)调控需平衡HAZ脆化与冷裂风险:①低CE钢(Ceq≤0.4%)采用自由热输入模式(15-35kJ/cm);②中高CE钢(0.4%<Ceq≤0.6%)实施限热输入(25-45kJ/cm)配合局部预热(100-150℃)。实验表明,Q390钢在热输入量28kJ/cm时,冲击韧性较45kJ/cm工况提升35%。
3.4.2 温度场管理手段
预热温度(T0)通过公式T0=1440Pcm-392(℃)计算确定,多层焊接时实施道间温度监控(Tinter= T0±20℃),采用红外热像仪实时反馈系统可降低温度波动至±5℃。对于δ≥50mm的18MnMoNb钢焊接,推荐采用阶梯预热工艺(200℃/2h→150℃/4h)。多层焊时应保证道间温度不低于预热温度,但也要避免道间温度过高导致韧性下降。
3.4.3 焊后热处理要求
焊后处理方案根据服役条件制定:①常规结构采用自然时效(t≥48h);②压力容器执行SR处理(580-620℃×2h+炉冷);③低温设备实施TMCP+回火(600℃×1h)。需特别注意含钒钢在600℃保温时存在二次脆化现象(t≤30min),可以采用两阶段处理:第一阶段580℃×2h消氢,第二阶段550℃×4h消应力。对于延迟裂纹敏感材料(σb≥690MPa),焊后需在4h内进行250℃×6h的后热缓冷处理。
结论
本文系统分析了热轧及正火钢的成分、性能、焊接性以及焊接工艺要点。研究结果表明:
①焊接性分析:热轧及正火钢具有良好的焊接性,但随着合金元素含量的增加,焊接性逐渐变差,主要表现为冷裂纹和热裂纹的敏感性增加。通过优化焊接工艺参数,如预热温度、焊接热输入和焊后热处理,可以有效降低裂纹的风险。
②热影响区性能变化:焊接过程中,热影响区的性能变化(如过热区脆化和热应变脆化)对焊接接头的力学性能有显著影响。通过控制焊接热输入和采用合适的焊接材料,可以有效改善热影响区的性能。
③典型钢种 Q345 的焊接工艺:Q345 钢的焊接工艺要点包括合理的预热措施、焊接材料选择和焊接参数控制。这些措施能够确保焊接接头的性能满足工程要求。
综上所述,热轧及正火钢的焊接技术需要综合考虑材料特性、焊接工艺参数和焊后处理等因素,以确保焊接质量和结构的安全性。未来的研究可以进一步探索新型焊接技术和材料优化,以提高焊接效率和接头性能。
参考文献
[1]戴为志.影响钢结构焊接技术进步的几个重要因素[J].电焊机,2020,50(09):207-212.
[2]高良,周云芳,戴为志.建筑钢结构高强钢不适合大线能量焊接[J].电焊机,2016,46(02):1-6.
[3]任宝雷,刘家富.海洋平台焊接技术现状及未来发展方向研究[J].中国石油和化工标准与质量,2022,(19):166-167.
[4]潘彦江.现代焊接技术的种类及应用特征[J].农机使用与维修,2022,(10):70-72.
[5]刘宝强.天然气管道施工焊接技术措施分析[J].当代化工研究,2022,(14):12-14.
[6]闫涛.优化天然气管道施工焊接技术策略研究[J].城市建筑空间,2022,(S1):243-244.
作者简介:李明霞,1976.11-,女,汉,中级教师,研究方向:焊接
如何引用
参考
戴为志.影响钢结构焊接技术进步的几个重要因素[J].电焊机,2020,50(09):207-212.
高良,周云芳,戴为志.建筑钢结构高强钢不适合大线能量焊接[J].电焊机,2016,46(02):1-6.
任宝雷,刘家富.海洋平台焊接技术现状及未来发展方向研究[J].中国石油和化工标准与质量,2022,(19):166-167.
潘彦江.现代焊接技术的种类及应用特征[J].农机使用与维修,2022,(10):70-72.
刘宝强.天然气管道施工焊接技术措施分析[J].当代化工研究,2022,(14):12-14.
闫涛.优化天然气管道施工焊接技术策略研究[J].城市建筑空间,2022,(S1):243-244.
版权
未提供许可协议