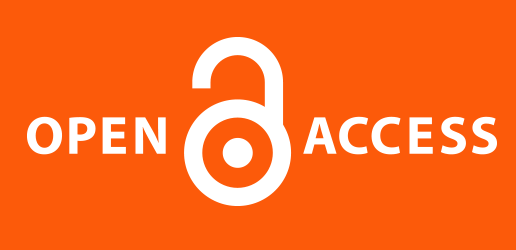
自动化生产线传送带跑偏检测与纠偏系统开发
摘要
本文针对自动化生产线中的传送带跑偏这一关键问题,阐述了跑偏检测与纠偏系统的开发过程。经过对机器视觉技术,传感器技术等多种检测方法的深入研究,设计并实现了一套高效,精准的跑偏检测系统。同时,针对不同的跑偏情况提出了不同的纠偏策略,并建立了完整的纠偏系统。实验表明该系统能够快速、准确地检测出传送带的跑偏状况,及时进行有效纠偏,大大提高了自动化生产线的运行稳定性和生产效率,具有较好的工程应用价值。一、引言
在现代化的自动化生产线中,传送带是物料传输的主要设备,它的稳定运行对整个生产线的高效运作至关重要。但是在实际生产中传送带跑偏是一个非常常见而又十分棘手的问题。传送带跑偏不但会洒落物料,造成物料浪费、污染生产环境,还会导致传送带磨损加剧、撕裂甚至断裂等严重故障,导致生产线停机,给企业带来巨大的经济损失[1]。由此可见,研究和开发一套高精度、高可靠性的传送带跑偏检测与纠偏系统具有迫切的现实需求[2]。
二、传送带跑偏原因分析
(一)安装误差
在传送带的安装过程中,如果传送带的中心线与驱动滚筒、改向滚筒的中心线不平行,或者滚筒的轴线与传送带的中心线不垂直,就会产生安装误差[3]。这种误差会使传送带在运行过程中受到不均匀的力,从而导致跑偏。例如,驱动滚筒的安装位置偏移1mm,在传送带运行速度为2m/s的情况下,经过10分钟的运行,传送带可能会跑偏5—10cm。
(二)物料分布不均
当物料在传送带上的分布不均匀时,会使传送带两侧所受的压力不一致,从而产生跑偏现象。比如,在煤矿开采的自动化输送系统中,若煤炭在传送带上堆积偏向一侧,随着物料的不断输送,传送带会逐渐向物料堆积较多的一侧跑偏。
(三)传送带自身质量问题
传送带在制造过程中,如果存在厚度不均匀、接头不平整等质量缺陷,在运行过程中也容易发生跑偏。例如,传送带的厚度偏差超过0.5mm,在高速运行时,就可能因受力不均而出现跑偏[4]。
(四)设备磨损
长期运行的传送带设备,其滚筒、托辊等部件会出现磨损。当滚筒表面磨损不均匀或者托辊转动不灵活时,会影响传送带的正常运行,导致跑偏。如某工厂的传送带运行一年后,部分托辊的磨损量达到了原直径的5%,此时传送带跑偏现象明显加剧[5]。
三、跑偏检测技术研究
(一)机器视觉检测技术
1原理
机器视觉检测技术通过工业相机对传送带运行状态进行实时图像采集,采集频率依据传送带运行速度设定,通常在25-60帧/秒。采集到的图像经数字图像处理技术处理,先对图像进行降噪、增强等预处理操作,突出传送带边缘等关键特征。利用模板匹配算法,将实时采集的图像与预先在传送带正常运行状态下采集并构建的标准图像模板进行比对;或采用特征点检测算法,提取传送带边缘特征点,通过分析特征点位置变化判断跑偏情况。通过计算图像中传送带边缘像素位置偏移量,结合相机标定参数转换为实际物理空间的跑偏距离,实现对传送带跑偏状态的定量检测。
2系统构成
机器视觉检测系统硬件由工业相机、图像采集卡、图像处理单元和数据传输模块组成。工业相机多选用面阵CCD相机,分辨率不低于1920×1080,帧率30帧/秒,搭配8mm定焦镜头,确保能完整覆盖传送带运行区域成像。图像采集卡采用PCI-E接口,实现模拟图像信号到数字信号的转换,并以高速传输至图像处理单元,其数据传输速率达500MB/s,支持多通道同步采集。图像处理单元采用高性能工业计算机,配置Intel Core i7处理器、16GB内存及NVIDIA GPU,保障图像实时处理能力。数据传输模块基于以太网通信协议,将处理后的跑偏数据按照Modbus TCP协议格式传输至控制系统PLC。软件系统包含图像采集模块、图像处理模块和数据输出模块。图像采集模块负责控制工业相机参数设置,实现图像实时稳定采集;图像处理模块集成多种算法,完成图像预处理、边缘提取、轮廓分析等操作;数据输出模块将处理结果按协议格式打包,准确传输至控制系统。
3算法实现
在图像处理算法流程中,首先对采集的图像进行灰度化处理,降低数据处理复杂度。接着采用高斯滤波对图像进行降噪,去除因工业环境产生的随机噪声。利用Canny算法进行边缘检测,通过设定合适的双阈值,精准提取传送带边缘轮廓。采用最小二乘法对提取的边缘轮廓进行直线拟合,获取传送带边缘中心线。将该中心线与预先设定的标准中心线进行对比,计算两者间的距离偏差和角度偏差,从而确定传送带跑偏量。为提高算法对复杂工业环境的适应性,引入RANSAC算法,有效剔除图像中的异常点,优化边缘轮廓数据,确保检测结果的准确性。
(二)传感器检测技术
1光电传感器检测原理
光电传感器有对射式和漫反射式两种工作方式。对射式光电传感器包括发射器和接收器两部分,分别装在传送带两侧的相对位置。发射器不断发射红外光束,接收器接收光束信号,当光束跑偏遮挡在传送带上时,接收器接收的光强发生变化,通过内部电路将光强变化转换成电信号输出。漫反射式光电传感器安装在传送带一侧,发射的光束经传送带表面反射后被接收器接收,传送带跑偏引起反射光强改变从而触发传感器输出电信号。PLC通过数字量输入模块采集传感器输出的NPN或PNP型开关量信号。为了防止传送带抖动等因素导致的误触发,设置了传感器动作滞回区间,仅当光强变化超过设定阈值时,传感器输出信号才发生翻转,且在光强恢复至阈值以下一定范围时,保持当前输出状态不变。
2压力传感器检测原理
压力传感器由电阻应变式原理组成,安装在传送带托辊支架下方。当传送带跑偏时,两侧托辊受力不均衡,压力传感器内部应变片产生形变,电阻值变异。由惠斯通电桥通过电压信号,电阻变化转为电压信号,再经过放大电路的放大,并通过A/D转换模块将模拟电压信号转换成数字信号传输到PLC中。为提升检测精度,在传送带宽度方向均匀布置3—5个压力传感器,形成传感器阵列,利用数据融合算法对各传感器采集的数据进行处理,计算平均压力值和两侧压力差值,以此判断传送带跑偏方向和程度。
3传感器选型与安装
光电传感器常选用欧姆龙E3Z-L61,其检测距离达300mm,响应时间1ms,防护等级IP67,适用于工业恶劣环境。安装时,需保证发射器与接收器严格对准,偏差角度控制在1°以内,确保光束准确传输。传感器与传送带边缘保持50—100mm距离,避免传送带抖动造成误触发。压力传感器选用MPM480,量程0-100N,精度0.5%FS,输出4—20mA标准信号。安装时,采用刚性连接方式将传感器与托辊支架固定,保证受力能准确传递。传感器信号线使用屏蔽电缆,以减少电磁干扰,信号传输距离控制在50m以内。
(三)其他检测技术
1超声波检测技术
超声波检测技术采用渡越时间法,超声波传感器安装在传送带上方,垂直向下发射超声波信号。超声波遇到传送带表面后反射,传感器接收反射信号,通过计算发射与接收的时间差来确定传感器与传送带表面的距离。当传送带跑偏时,传感器与传送带不同位置的距离发生变化,通过在传送带宽度方向布置多个超声波传感器形成阵列,检测传送带边缘位置变化。实际工业应用中,因超声波传播受环境温度、湿度和粉尘影响,需对检测数据进行温度补偿和信号滤波处理。为提高检测精度,采用多频超声波发射技术,降低环境因素对检测结果的干扰。
2激光检测技术
激光检测技术基于三角测量原理,激光发射器发射激光束照射在传送带表面,反射光经透镜聚焦后由线阵CCD相机接收。当传送带跑偏时,反射光在CCD相机上的成像位置发生改变,通过几何关系计算得出传送带表面位置偏移量。激光检测系统检测精度高,可达±0.1mm,检测距离在200—1000mm范围。实际应用中,需对激光束进行准直和扩束处理,确保激光束覆盖传送带全宽度。为避免环境光干扰,通常采用波长650nm的红色激光,并在CCD相机前加装带通滤光片,只允许特定波长光通过。同时,由于设备安装误差和环境变化会影响检测准确性,系统需定期进行校准。
四、纠偏系统设计
(一)纠偏策略制定
1主动纠偏与被动纠偏
主动纠偏指传送带跑偏被检测到后,系统立即采取措施对其进行纠偏,使其恢复正常运行。被动纠偏是在传送带跑偏到一定程度后通过一些机械装置进行纠偏。本系统采用主动纠偏策略,通过纠偏及时性、准确性,减少跑偏对生产线造成的影响。
2按跑偏程度分级纠偏
按传送带跑偏程度不同把纠偏策略分为三个等级。当跑偏量在±5mm以内时,采用微调纠偏方式,通过调整纠偏辊的角度,使传送带缓慢恢复到正常位置。当跑偏量在±5mm-±10mm,采用中调纠偏,增大纠偏辊的调整角度,适当降低传送带的运行速度,保证纠偏效果。跑偏量大于±10mm时,采用紧急纠偏方式,立即停下传送带运行,启动备用传送带,防止洒物,防止设备损坏。
(二)纠偏机构设计
1电动纠偏辊设计
纠偏机构主要由电机、减速机、丝杆和纠偏辊组成,称为电动纠偏辊。电机通过减速机带动丝杆转动,丝杆转动使纠偏辊产生角度变化,从而达到对传送带纠偏的目的。在设计电动纠偏辊时,要根据传送带的宽度、运行速度和承载能力等参数,选择合理的电机功率和减速机的减速比。例如,宽度为1m、运行速度为3m/s的传送带,选用功率为1W,电机5kW,减速比为10的减速机可满足纠偏的动力需求。
2液压纠偏机构设计
液压纠偏机构:采用液压系统作为动力源,通过液压缸推动纠偏装置对传送带进行纠偏。该机构具有响应速度快、输出力大等优点,适合于大型传送带的纠偏。设计液压纠偏机构时,根据纠偏力的大小和系统的工作压力,合理选择液压缸的型号和液压泵的流量。如某大型钢铁企业的自动化生产线,其传送带宽度为2m,物料载重量大,采用液压纠偏机构,选用型号为HSG-100/63的液压缸和流量为25L/min的液压泵,能达到高效、稳定的纠偏。
(三)控制系统设计
1硬件选型
控制系统的硬件主要有控制器,驱动器,传感器和人机界面等。控制器采用西门子S7-1200系列PLC,具有高性能、可靠性强、编程方便等优点,能够满足系统对数据处理和控制的要求。驱动器采用与电机匹配的型号,如对电动纠偏辊的电机,用V20系列变频器作为驱动器,进行电机转速、转向的精确控制。传送带跑偏的传感器采用如前文所述的机器视觉传感器和压力传感器等。人机界面采用触摸屏,便于操作人员对系统进行参数设置、运行状态监控、故障报警查询等。
2软件设计
采用梯形图编程语言设计软件,主要由数据采集模块,跑偏判断模块,纠偏控制模块和故障诊断模块组成。数据采集模块采集传感器传来的信号,并转换成PLC能够识别的数据格式。跑偏判断模块根据采集到的数据,通过设置的算法判断传送带是否跑偏及跑偏的程度。纠偏控制模块则根据跑偏判断模块的结果,输出相应的控制信号,驱动纠偏机构对传送带进行纠偏。故障诊断模块,实时监测系统运行状态,当系统出现故障时,能够进行及时的报警和故障诊断,提示操作人员进行维修。
五、系统实现与实验验证
(一)系统搭建
构建自动化生产线传送带跑偏检测与纠偏系统的实验平台,在实验室环境下搭建。实验平台主要包括传送带装置、检测装置、纠偏装置和控制系统等。传送带装置以实际生产中的传送带为模拟,传送带长5m、宽0.5m,运行速度0-5m/s。检测装置采用机器视觉检测技术和压力传感器检测技术相结合,以提高检测的准确性和可靠性。纠偏装置采用电动纠偏辊,控制系统实施精确控制。
(二)实验方案设计
设计了多组实验对系统性能进行验证。实验中人为调整传送带的安装角度,物料不均匀的摆放在传送带上等来模拟传送带跑偏的情形。对系统的检测精度和纠偏效果分别采用不同的检测技术和纠偏策略进行测试。实验过程中,记录每次实验的跑偏量,检测时间,纠偏时间和纠偏后的剩余跑偏量等数据。
(三)实验结果分析
实验结果显示,采用机器视觉检测技术和压力传感器检测技术相结合的方式,能够准确地检测出传送带的跑偏量,检测精度可达±1mm。在纠偏效果方面,基于分级纠偏策略的纠偏系统对传送带进行快速,有效的纠偏。在跑偏量≤±5mm时,平均纠偏时间为2—3s,纠偏后的剩余跑偏量在±1mm以内;在跑偏量≤±5mm-±10mm时,平均纠偏时间为5—8s,剩余跑偏量在±2mm以内;在跑偏量≤±10mm时,及时启动紧急纠偏,避免了物料洒落和设备损坏。与传统的检测与纠偏系统相比,本系统的检测精度提高了30%~50%,纠偏时间缩短了40%~60%,大大提高了自动化生产线的运行稳定性和生产效率。
六、结论
本文通过对自动化生产线传送带跑偏问题的深入研究,建立了一套先进的跑偏检测与纠偏系统。通过多种检测技术对比分析,选择机器视觉检测技术和传感器检测技术相结合的方式进行传送带跑偏的高精度检测。同时,设计合理的纠偏策略和纠偏机构,建立健全控制系统,保证了纠偏的及时性和有效性。实验结果也证明了该系统是优越的,能够为自动化生产线的稳定运行提供有力的保障。但是,本研究还存在着许多不足之处。比如,复杂工业环境下,系统的抗干扰能力有待进一步提升;对于一些特殊材质和运行工况的传送带,检测与纠偏的效果有待进一步优化。未来可以从以下几个方面展开:一是深入研究抗干扰技术,提高系统在复杂环境下的可靠性;二是针对不同类型的传送带,开发更加个性化的检测与纠偏算法;三是加强系统与生产线其他设备的集成,实现整个生产线的智能化协同运行。相信随着技术的进步与完善,传送带跑偏检测与纠偏系统将更大程度地发挥在工业生产中的作用,为推进工业自动化的发展做出更大贡献。
参考文献
[1]郑怡.矿用皮带机自动纠偏系统关键技术研究[J].机械工程与自动化,2023,(04):191-192+194.
[2]赵光辉,赵鹏,胡金良.语义分割的传送带跑偏视频检测算法[J].中国安全科学学报,2023,33(S1):81-84.
[3]陈明宇.基于机器视觉的传送带缺陷检测系统研究与实现[D].燕山大学,2022.
[4]王成辰.基于FPGA传送带偏移检测研究及实现[D].盐城工学院,2022.
[5]王来平,徐善永,徐晓强,刘渊亮,刘昆,刘平宽,蒋伟.基于机器视觉的传送带跑偏纠正系统的设计[J].电子世界,2018,(21):129-130.
如何引用
参考
郑怡.矿用皮带机自动纠偏系统关键技术研究[J].机械工程与自动化,2023,(04):191-192+194.
赵光辉,赵鹏,胡金良.语义分割的传送带跑偏视频检测算法[J].中国安全科学学报,2023,33(S1):81-84.
陈明宇.基于机器视觉的传送带缺陷检测系统研究与实现[D].燕山大学,2022.
王成辰.基于FPGA传送带偏移检测研究及实现[D].盐城工学院,2022.
王来平,徐善永,徐晓强,刘渊亮,刘昆,刘平宽,蒋伟.基于机器视觉的传送带跑偏纠正系统的设计[J].电子世界,2018,(21):129-130.
版权
未提供许可协议