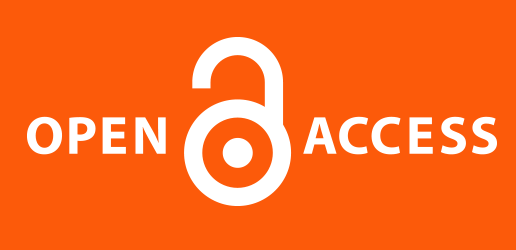
化工企业循环水系统节水节能技术改造研究
摘要
本研究针对石化企业循环冷却水系统的高能耗、高水耗问题,系统分析了开式与闭式循环系统的技术特点及应用优势。研究表明,通过优化循环水系统运行参数、提升浓缩倍数、实施废水回用等综合措施,可显著提高水资源利用效率。重点探讨了变频调速技术在循环水系统中的节能机理与应用效果,验证了其在降低能耗、延长设备寿命方面的突出优势。结合某石化企业实际案例,证实了循环水系统节水节能改造在经济效益和环境保护方面的双重价值,为行业绿色转型提供了技术参考。1 石化企业循环冷却水系统
1.1 开式循环冷却水系统
利用冷却塔实现散热的开式循环水系统能够高效完成水的重复利用。该系统的核心构成部件包括通风塔、喷淋装置、布水机构、集水槽以及风机等设备,其中喷淋塔在系统中起着举足轻重的作用。喷淋塔通过将高温水流破碎成细密水珠或形成薄水膜,从而大幅提升热交换效率。开式循环系统在散热时会与大气产生直接接触,造成部分冷却水因汽化而损耗,进而导致循环水中的盐分持续累积。为保证系统正常运行,需要定期补充新水并排出部分浓缩水,以维持水质稳定和水量平衡。在高温季节,由于环境温度较高,汽化散热和辐射散热效果较为明显;而在寒冷季节,得益于低温环境,传导散热的作用更为显著。
1.2 闭式循环冷却水系统
闭式循环冷却水系统采用完全封闭的回路运行方式,冷却水在使用后不会外排,而是重新回流至系统进行循环利用。这类系统通常需要配合其他热交换装置共同工作,通过完全密封的运行模式显著降低水资源的损耗。在内燃机、发电机组等设备的温度控制环节,闭式循环冷却水系统具有广泛的应用价值,既能确保设备可靠运转,又可实现水资源的节约利用。
2 循环水系统节水技术应用优势分析
2.1 水资源节约策略
以循环冷却水系统的水资源消耗为研究重点,提出了减少渗漏与蒸发损耗、优化循环水利用率以及降低补水频率等多项节水方案。循环水系统的节水工作不仅是提升能源效率的技术手段,更是实现低碳减排、保护生态环境的重要举措,对我国经济的绿色可持续发展具有深远影响。相较于传统的一次性供水模式,循环冷却水系统展现出显著的节水优势与资源利用效率[1]。通过循环水的重复使用,并整合反渗透膜工艺、生物膜处理、膜分离技术以及现代化水处理工艺,能够显著提高水资源的综合利用率,同时降低对生态环境的负面影响。在当前全球水资源日趋紧张、环保标准不断提高的形势下,加强循环水系统节水技术的创新与实践,已成为化工行业实现绿色转型的必由之路。
2.2 浓缩倍数优化措施
提升循环水系统的浓缩倍数是实现节水目标的核心途径之一,该方法能够有效提高循环水的含盐量,从而减少淡水资源的消耗。在常规的直流冷却水处理方式中,由于采用一次性用水模式,必须持续补充新水,且补充水源通常需要采用优质淡水。与之相比,循环水系统能够充分利用再生水和循环回用水,并通过科学的净化工艺使其达到回用标准。在此过程中,可通过改进冷却塔的热回收性能、优化水质与温度控制策略以及科学投加化学药剂等方法,显著提高冷却水的循环利用率,最终实现节水增效的目的。在循环冷却水系统中推广应用节水技术,不仅能够大幅降低企业的运营成本,还能显著减少对生态环境的压力,实现经济效益与生态效益的协同提升。
2.3 废水回用与资源化技术
废水回收与资源化利用是水资源可持续管理的重要技术手段,特别是在水资源日益匮乏的背景下,对工业废水进行高效处理与循环利用,对于减轻环境负担和降低企业运营成本具有重要价值。在化工生产过程中,工业废水通常含有复杂的污染物,包括有机化合物、重金属离子、氨氮等有害成分,因此必须采用科学的预处理工艺,去除废水中的有害物质,使其达到工业回用水质标准。目前广泛应用的废水资源化技术包括反渗透(RO)工艺、离子交换法、膜分离技术等[2]。反渗透技术作为一种高效的膜分离工艺,利用选择性渗透膜的特性,能够有效截留废水中的溶解性盐类、有机污染物以及微生物等杂质。通过施加外部压力,水分子可选择性透过膜层,而污染物则被有效截留,从而获得高纯度的再生水。离子交换技术主要用于去除废水中的可溶性离子污染物,如钙镁等致垢离子或毒性重金属离子。该技术通过特定功能树脂与废水中的目标离子发生置换反应,实现有害成分的高效去除。膜分离技术则利用不同孔径规格的膜材料,可有效去除废水中的固体悬浮物、胶体颗粒以及大分子有机物,通常作为预处理工艺与反渗透技术联用,以满足更高标准的回用水质要求。
以某大型化工企业为例,该企业实施了工业废水循环利用示范工程,针对含有高浓度有机物、重金属及氨氮等污染因子的生产废水进行综合处理,使处理后的再生水能够重新投入生产流程循环使用。经实际运行数据表明,该处理工艺使废水中的化学需氧量(COD)指标降低近70%,氨氮污染物去除率达到85%以上,整体废水回用率突破70%的技术指标。为进一步提升水质标准,该企业还引入了先进的膜分离系统对污水进行深度净化处理。采用膜分离工艺后,系统对COD的截留效率提升至90%,氨氮去除效果达到99.5%的行业领先水平,总磷去除率同样高达99.2%,最终产水完全符合工业循环冷却水的各项水质标准。实践表明,化工行业通过实施循环水系统节水技术,特别是废水资源化利用工程,已成为实现水资源可持续利用的战略性举措。该技术体系不仅能大幅削减废水排放量和水资源消耗,还在降低生产成本的同时有效保护生态环境,成功实现了经济效益与环境效益的有机统一。
2.4 节水节能协同优化技术
通过实施循环水系统的精细化管理和工艺升级,可显著降低企业的水资源需求。经处理后的再生水可实现梯级利用,从而最大化水资源利用效率。现代循环水系统技术不仅能够提高水的重复利用率,还能同步降低企业能源消耗和运行费用[3]。对关键设备如循环水泵、换热器等进行技术升级和运行优化,可有效降低系统能耗,提升能源转换效率,最终达成节能降耗的运营目标。因此,循环水系统的节能改造既是资源节约的重要措施,也是提升企业经济效益的有效手段。特别是在化工生产领域,采用循环水系统实现节水与节能的协同优化,在减少水耗和能耗方面展现出显著的技术优势和应用价值。
2.4.1 变频驱动技术应用
采用智能变频控制系统可根据实际工况需求动态调节水泵转速,实现显著的节能效果。某化工企业应用案例显示,原水泵机组运行功率为117kWh,经变频改造后系统总能耗降至72kWh,综合节能效率达到39%。
2.4.2 精密过滤技术创新
运用微孔过滤元件与陶瓷膜组件等新型过滤介质,可高效截留水中的悬浮物和微生物,大幅改善出水水质并避免二次污染。某石化企业实施案例表明,采用该技术后中水回用率由40%提升至60%,且处理后的高品质再生水可直接作为锅炉补给水,节水效益显著。
2.4.3 高效浓缩工艺突破
新型浓缩技术可实现高倍率水分回收,最大限度降低系统水损,提高再生水产出率。在某大型石化企业的工程实践中,应用该工艺后系统水回收率从60%跃升至80%,整体用水量减少20%,节水效果突出。
3 化工企业循环水系统节电技术分析
3.1 变频节能技术运行机理
变频节能技术依托电力电子转换与自动控制原理,借助变频装置对水泵驱动电机实施精准转速调控,达成循环水系统供排水平衡的动态适配。该技术系统由压力/流量检测单元、智能控制中枢、变频驱动模块及执行机构共同组成:在循环水主管道的进出水端分别配置高精度压力传感器和超声波流量计,持续获取系统运行状态参数;智能控制单元集成自适应PID算法,将实时监测数据与预设参数进行比对后产生脉宽调制信号,控制功率半导体器件调整电机供电频率,实现水泵转速在30%-100%范围内的连续可调。针对化工生产装置负荷周期性变化特点,系统配置多工况运行模式——在夜间生产低谷时段自动转入低频节能状态,生产高峰时段智能提升运行频率确保供水压力恒定,彻底规避传统阀门调节带来的能量浪费[4]。
此项技术能够有效解决传统水泵系统供水量过剩、频繁启停等运行弊端,大幅降低系统能耗与运营支出。同时,变频调速装置还可减少水泵机械磨损,延长设备服役周期,并提升整体系统运行可靠性。相关研究数据表明,变频调速技术在化工行业的应用可使循环水系统能耗降低20%-30%,同时提升供水效率15%-25%。以某大型石化企业实际运行数据为例,引入变频节能技术后,循环水系统综合能耗平均下降26.8%,水泵设备使用寿命明显延长,系统运行稳定性获得显著提升。
3.2 变频调节技术实施方案
在化工生产领域,采用变频调速技术调控水泵运行工况,以实现节能降耗目标。具体技术路线如下:
3.2.1 智能变频泵组控制:
循环水系统中,采用矢量控制型变频器与水泵电机直接耦合,通过调节输出电源特性实现电机转速的精确控制。系统集成压力传感网络与流量监测装置实时采集管网运行参数,结合改进型PID闭环控制策略动态优化变频器输出。当生产负荷降低时,变频器自动将输出频率从额定50Hz调整至30-40Hz区间,使水泵转速相应降低,流量呈线性关系递减,而功率消耗则遵循转速三次方关系显著下降。此外,变频器内置的软启动功能可将启动电流控制在额定电流1.2倍范围内,有效避免传统直接启动时5-7倍冲击电流对配电系统的扰动,大幅延长电机与机械密封组件的使用寿命。
3.2.2 系统参数协同优化:
基于流体力学原理建立系统水力模型,利用数值仿真平台对泵组性能曲线与管网特性曲线进行匹配度分析。通过优化泵的额定功率参数、改进叶轮水力设计及调整管道局部阻力系数,将水泵工作点从低效运行区迁移至最佳效率区间。针对多泵并联系统,实施"主频跟踪+辅频补偿"的智能控制策略:主泵依据总管压力反馈信号自动调节运行频率,辅泵根据流量偏差值智能启停,并应用模糊预测算法预判负荷变化趋势,提前0.5-1秒进行频率预调节,有效消除传统离散调节方式导致的压力波动现象。
3.2.3 管路节流装置加装:
在循环水输送管道中增设节流元件,如孔板节流装置或调节阀门等,以调控流体流速,实现附加节能效果。这些节流装置不仅能有效降低水泵运行负荷,还可实现显著的能耗节约,同时具备流量微调功能[5]。
通过上述技术措施的综合实施,化工企业循环水系统的节能成效得到明显提升。以某中型化工企业改造项目为例,应用变频调速技术后,循环水系统年耗电量从120万千瓦时降至约90万千瓦时,年度电费支出减少近30万千瓦时,同时水泵设备故障率明显下降,维护成本大幅降低。由此可见,采用变频调速技术实施化工企业节能改造,不仅技术可行,而且经济效益显著。
4 具体案例分析
4.1 工程概况
某大型石油化工企业针对其循环水系统存在的高能耗、高水耗问题,开展了综合性的节水节能技术改造工程。在节水技术应用方面,创新性地采用双级反渗透膜分离工艺,将循环冷却系统排放的含盐废水首先输送至预处理单元,随后通过高压泵加压进入反渗透膜组件进行深度处理,实现日均8000m3的浓盐水净化回用,成功替代原系统30%的工业新鲜水补充需求。在节能改造方面,部署了智能化变频调控系统,为12台主循环水泵配备高性能矢量变频装置,依托PLC控制系统实时采集管网压力和水温参数,运用PID闭环调节算法动态优化电机转速,使水泵运行能效由改造前的62%显著提升至88%。同时,采用新型高分子纳米复合材料对4台处理能力为5000m3/h的逆流式冷却塔填料进行表面处理,配套安装自动旋转式喷淋清洗设备,将气水比参数从0.8优化调整至1.2,使换热效率整体提升25个百分点。
4.2 运行成效
技术改造工程实施后取得显著效益:在节水方面,年均可节约工业用水326万吨,减少新鲜水采购费用780万元;在节能方面,通过变频调速和冷却塔性能提升,年节电量达到1260万千瓦时,相当于节约标准煤4200吨,减少二氧化碳排放10800吨;在环保方面,反渗透系统产生的浓盐水经过蒸发结晶工艺处理后,系统废水排放总量降低82%,出水COD和总磷浓度分别控制在15mg/L和0.3mg/L以下,各项指标均优于《污水综合排放标准》中最严格的一级A标准。该技术改造项目总投资回收周期仅为2.3年,被评选为省级工业节水示范项目,为石油炼化行业循环水系统的绿色低碳改造提供了可推广、可复制的技术解决方案和实践经验。
5 结语
综上所述,本研究系统论证了循环水系统节水节能改造的技术可行性和经济合理性。实践表明,通过优化系统运行参数、应用先进处理工艺和实施智能化控制,可显著提升水资源和能源利用效率。这些技术措施不仅降低了企业运营成本,还减少了环境污染,实现了经济效益与生态效益的协同发展。研究成果为石化行业循环水系统升级提供了重要参考,对推动工业绿色转型具有积极意义。
参考文献
[1]叶晓林,赵玥,孙飞.炼化企业污水回用至循环水系统的分析研究[J].给水排水,2024,60(05):66-72.
[2]关勇,一种节水式循环冷却水化学和电化学协同处理技术.河北省,河北利源环保科技有限公司,2022-09-06.
[3]史载辉.循环冷却水工艺在化工企业的应用[J].石化技术,2021,28(03):31-33.
[4]司昌昆.石化企业循环水系统节能优化研究[D].中国石油大学(北京),2020.
[5]宋伟刚.化工企业循环水系统节水节能技术改造分析[J].化工设计通讯,2021,47(08):153-154+158.2.
作者简介:朱浩(1974—),男,汉族,江西省景德镇市人,研究方向为化工节能。
如何引用
参考
叶晓林,赵玥,孙飞.炼化企业污水回用至循环水系统的分析研究[J].给水排水,2024,60(05):66-72.
关勇,一种节水式循环冷却水化学和电化学协同处理技术.河北省,河北利源环保科技有限公司,2022-09-06.
史载辉.循环冷却水工艺在化工企业的应用[J].石化技术,2021,28(03):31-33.
司昌昆.石化企业循环水系统节能优化研究[D].中国石油大学(北京),2020.
宋伟刚.化工企业循环水系统节水节能技术改造分析[J].化工设计通讯,2021,47(08):153-154+158.2.
版权
未提供许可协议